Inseego's telematics business is now Ctrack
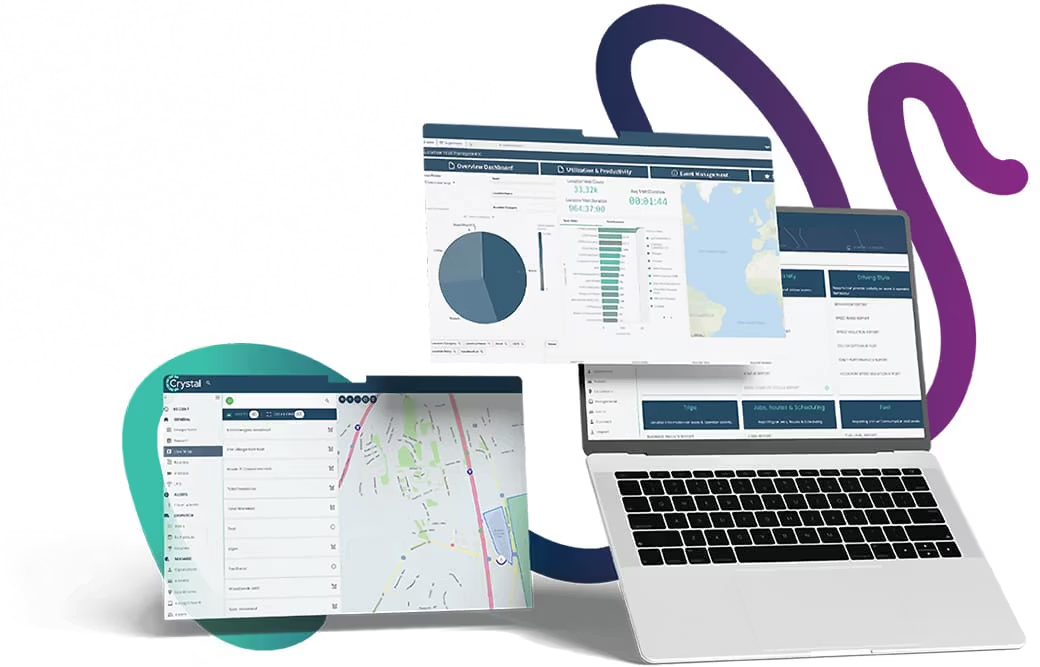
We are pleased to announce that Inseego's international telematics business is now part of Ctrack - a global leader in telematics, AI video and asset management solutions for nearly 40 years.
Even though this marks a new chapter, everything will remain business as usual – your existing contacts and services will remain unchanged. Our teams are working closely behind the scenes to ensure a smooth transition without disruption.
As we move forward, we look forward to providing you with even more powerful, data-driven solutions through Ctrack's advanced platform building on their decades of experience.